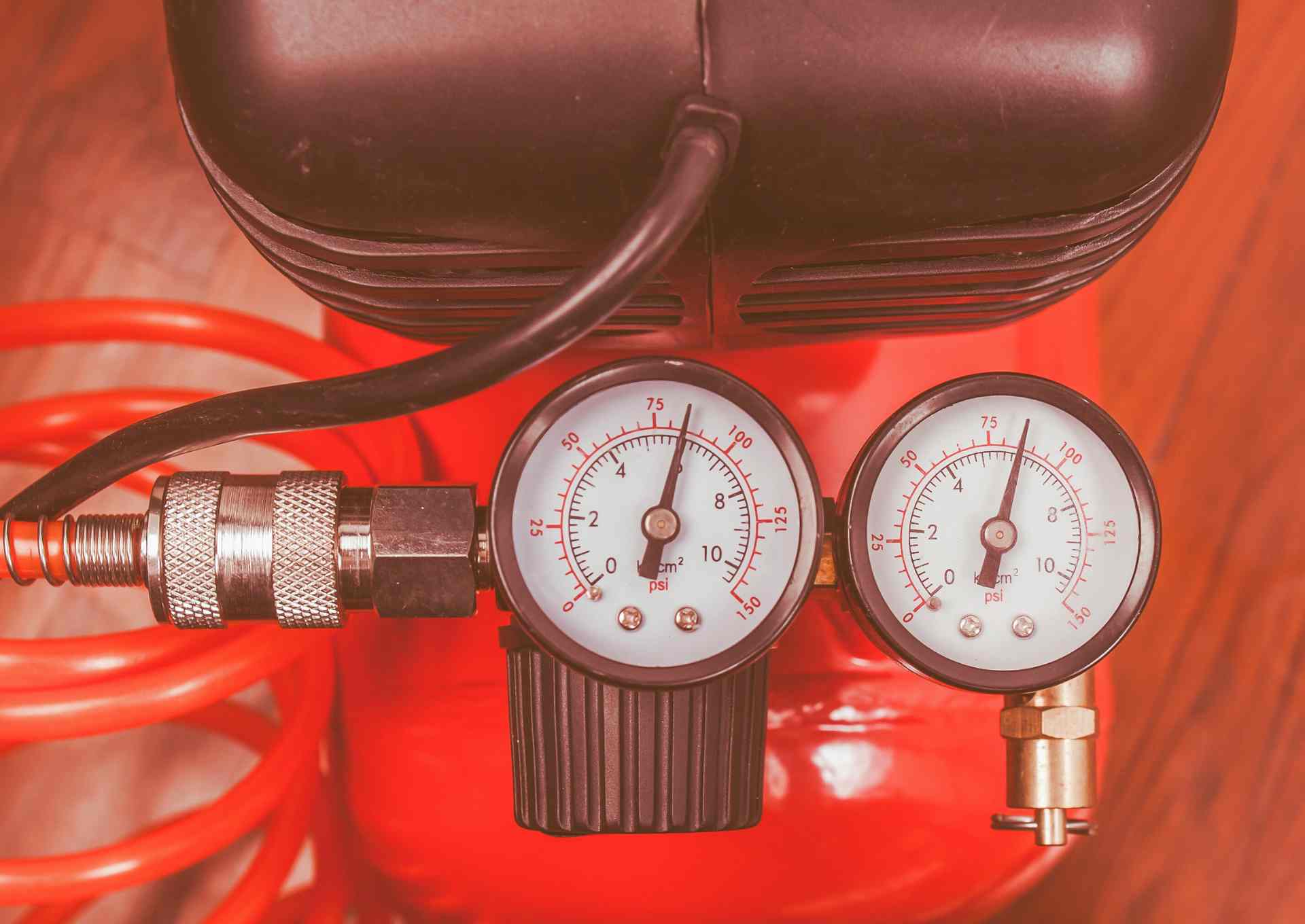
Technologia sprężonego powietrza na zawsze odmieniła oblicze przemysłu. Wydajne, mocne i skuteczne narzędzia i maszyny pneumatyczne to tylko niektóre zastosowania sprężarek i kompresorów. Niestety zdarza się, że instalacje sprężonego powietrza borykają się z problemem spadku ciśnienia, który znacząco obniża ich efektywność. Istnieją sposoby, aby temu zapobiec. Najpierw trzeba jednak poznać przyczyny spadku ciśnienia w instalacjach sprężonego powietrza.
Spadek ciśnienia w instalacji sprężonego powietrza – czym jest?
Spadki ciśnienia w instalacjach pneumatycznych to wbrew pozorom naturalny proces, który nierozerwalnie łączy się ze specyfiką pracy ze sprężonym powietrzem. Jednak warto pamiętać, że dobrze zaprojektowany system powinien utrzymywać straty ciśnienia poniżej… 10% ciśnienia wylotowego sprężarki! Przeskoczenie tej granicy może oznaczać, że do urządzeń zasilanych sprężonym powietrzem nie dociera odpowiednia jego ilość. Czym dokładnie jest taki spadek ciśnienia?
To zmniejszenie ciśnienia powietrza w układzie pneumatycznym, gdy powietrze przemieszcza się od wylotu sprężarki do punktu użytkowania. Zjawisko to występuje, gdy sprężone powietrze przemieszcza się przez system dystrybucji i może wystąpić na każdym etapie między wylotem sprężarki a końcowym zastosowaniem sprężonego powietrza.
Powody spadku ciśnienia w instalacjach sprężonego powietrza
- Zbyt długie rurociągi – długie rurociągi powodują większe tarcie powietrza o ścianki rur, a to z kolei zwiększa opory przepływu i prowadzi do spadku ciśnienia na końcach instalacji. Jednocześnie każda złączka, kolanko czy zawór w instalacji zwiększa opory przepływu oraz wydłuża drogę powietrza. Im więcej takich elementów, tym większe straty ciśnienia.
- Zły stan powierzchni wewnętrznych rur – zanieczyszczenia, osady i korozja wewnątrz rur również negatywnie wpływają na efektywny przepływ ciśnienia. Dotyczy to także zapchanych lub źle dobranych filtrów i separatorów, które montuje się wewnątrz rur.
- Nieszczelności – wycieki w przewodach sprężonego powietrza, spowodowane nieszczelnościami, to najczęstsze przyczyny spadków ciśnienia.
- Nieodpowiedni projekt instalacji – źle zaprojektowana instalacja, np. z nieodpowiednimi przekrojami rur czy nadmierną liczbą złączek również może powodować problemy z przepływem powietrza.
- Zbyt wysoka temperatura powietrza – jednym z najważniejszych parametrów w układzie sprężonego powietrza jest temperatura. To właśnie od niej zależy objętość powietrza. Zbyt wysokie wartości na termometrze powodują wzrost ciśnienia, a to z kolei powoduje wycieki sprężonego powietrza, które nie mieści się już w przewodach.
- Zły stan sprężarki – zużyta lub źle działająca sprężarka nie dostarcza powietrza o odpowiednim ciśnieniu, a to przekłada się na jego moc.
Spadek ciśnienia w systemach sprężonego powietrza – konsekwencje
Obniżone ciśnienie powoduje nieefektywne działanie urządzeń zasilanych sprężonym powietrzem. W rezultacie prowadzi to do szybkiego spadku wydajności pracy oraz wydłużenia czasu potrzebnego na realizację zadań. Zbyt niskie ciśnienie tworzy także nieodpowiednie warunki dla profesjonalnych maszyn, które przez brak odpowiedniej mocy mogą ulegać częstszym awariom, a nawet zniszczeniom.
Sytuacje te często wymuszają na użytkownikach konieczność zwiększenia ciśnienia wylotowego sprężarki, aby zrekompensować straty w systemie dystrybucji. To z kolei prowadzi do większego zużycia energii oraz podnosi koszty operacyjne i obniża efektywność energetyczną systemu. W efekcie przedsiębiorstwa muszą ponosić wyższe koszty eksploatacji sprężarek i całej infrastruktury sprężonego powietrza.
Kolejną konsekwencją jest wpływ na jakość produkcji. W niektórych procesach przemysłowych stabilne i odpowiednio wysokie ciśnienie sprężonego powietrza jest niezbędne do uzyskania produktów o odpowiednich parametrach. Spadki ciśnienia prowadzą do niestabilnej pracy maszyn, przez co znacznie obniża się jakość produkcji, zwiększa się ilość odpadów oraz wzrasta ryzyko przerw produkcyjnych.
Jak zapobiegać spadkom ciśnienia w instalacji sprężonego powietrza?
- Projektowanie i instalacja systemu – już na etapie projektowania należy zadbać o właściwe parametry instalacji, takie jak średnica rur, minimalizacja długości przewodów i unikanie zbędnych zakrętów oraz złączek, które mogą generować straty ciśnienia.
- Regularna konserwacja – regularne przeglądy i konserwacja systemu sprężonego powietrza są jednym z ważniejszych elementów prawidłowo działającej instalacji. Należy sprawdzać stan filtrów, uszczelek, zaworów i innych komponentów, które przy regularnym użytkowaniu szybko ulegają zużyciu lub zanieczyszczeniu, a to dodatkowo potęguje spadki ciśnienia.
- Używanie odpowiednich urządzeń – wybór wysokiej jakości komponentów i urządzeń, które są zaprojektowane z myślą o minimalizowaniu strat ciśnienia to podstawa efektywnej instalacji.
- Szkolenie personelu – zapewnienie odpowiedniego szkolenia dla personelu obsługującego systemy sprężonego powietrza jest istotne. Świadomość i umiejętność identyfikowania problemów oraz wykonywania podstawowych czynności konserwacyjnych może znacząco przyczynić się do zmniejszenia spadków ciśnienia.
FAQ:
1. Jakie są powody spadku ciśnienia w instalacjach sprężonego powietrza?
Spadek ciśnienia to częsty problem, który dotyczy wielu instalacji pneumatycznych. Najczęstsze powody to:
- nieszczelna instalacja,
- nieodpowiedni projekt instalacji,
- stara instalacja,
- zbyt długie rurociągi,
- zły stan rur.
2. Jakie są konsekwencje spadków ciśnienia w instalacji sprężonego powietrza?
Niskie ciśnienie powietrza negatywnie wpływa na efektywność produkcji. Może także pogorszyć jakość produktów oraz uszkodzić maszyny, które przeznaczone są do pracy na określonej mocy.