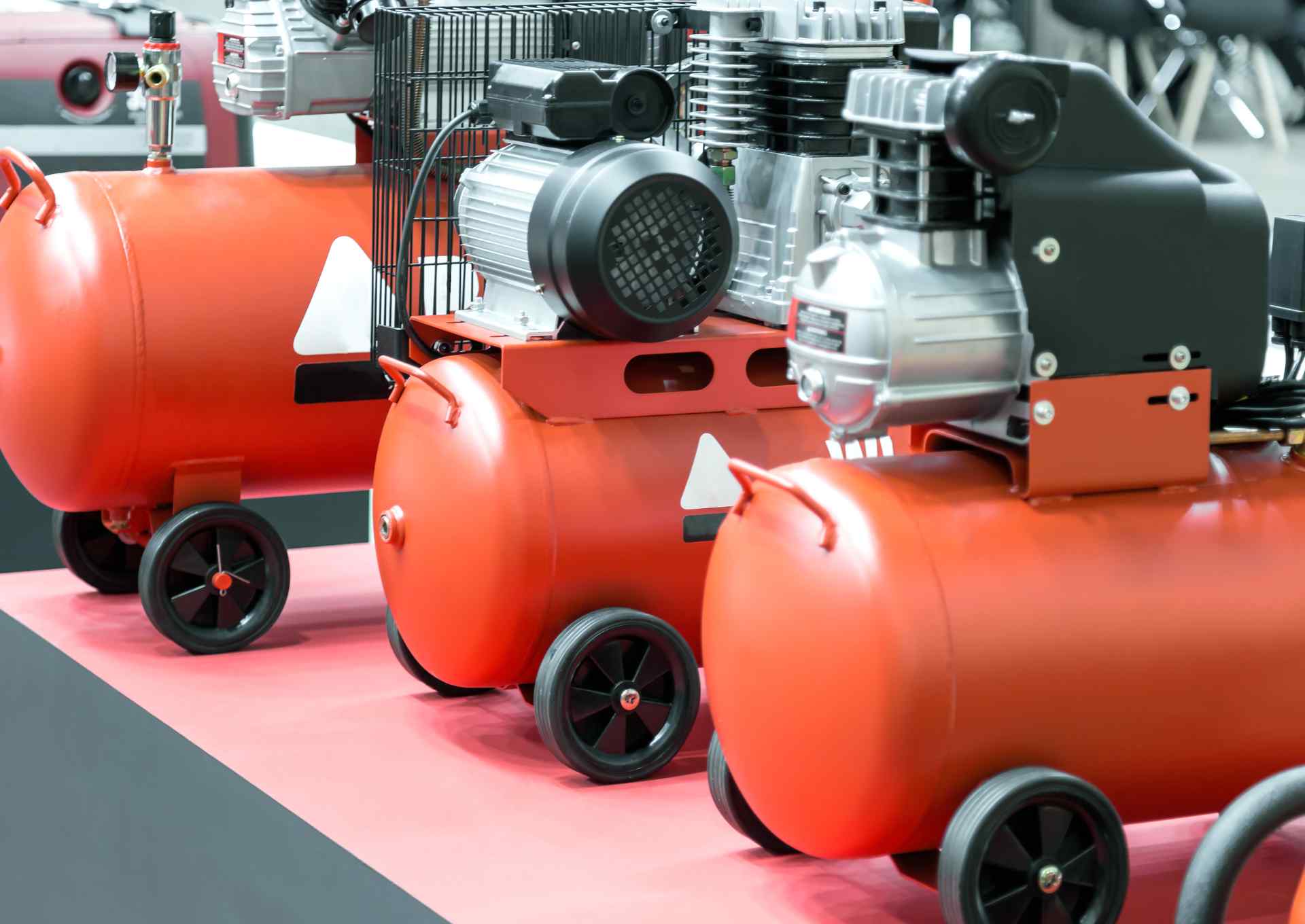
Audyt sprężonego powietrza staje się kluczowym elementem optymalizacji procesów przemysłowych w świecie. W jaki sposób przedsiębiorstwa mogą skorzystać z tego narzędzia, aby zidentyfikować potencjalne oszczędności i poprawić wydajność? Przedstawiamy, dlaczego i kiedy należy wykonać audyt sprężonego powietrza.
Audyt sprężonego powietrza – co to jest?
Audyt instalacji mającej dostarczyć gaz pod ciśnieniem ze sprężarki powietrza do urządzenia zasilanego pneumatycznie to klucz do prawidłowego funkcjonowania wszystkich systemów na hali produkcyjnej lub w innym zakładzie. Audyt instalacji sprężonego powietrza to usługa weryfikująca prawidłowe działanie systemu produkcji, dystrybucji i odbioru medium. W jej ramach realizuje się testy wszystkich elementów systemu pod względem wydajności, szczelności i dostosowania parametrów sprężonego gazu do wymagań odbiorników. W wyniku przeprowadzonych pomiarów wskazuje się zarówno poziom strat, jak i rozwiązania, które pozwolą na usunięcie nieprawidłowości.
Kiedy należy wykonać audyt sprężonego powietrza?
Jest kilka sytuacji, kiedy audyt sprężonego powietrza jest konieczny. Do takich kwestii należą m.in.:
- modernizacja instalacji,
- wdrożenie nowej instalacji
- spadek wydajności,
- nieuzasadniony wzrost kosztów eksploatacyjnych (w tym energii elektrycznej).
Wdrożenie nowej instalacji sprężonego powietrza wymaga sprawdzenia jej działania przed uruchomieniem. Audyt pomoże określić optymalne parametry i konfigurację systemu, aby zapewnić efektywność i oszczędności od samego początku. Audyt sprężonego powietrza może obejmować również wycieki powietrza, niewystarczającą regulację ciśnienia, nieprawidłową konfigurację sprężarek. Co więcej, jeśli zauważymy, że koszty poboru sprężonego powietrza staną się zbyt wysokie z nieuzasadnionych powodów, warto także zweryfikować działanie całego systemu. Audyt pomoże zidentyfikować, gdzie dochodzi do strat w zużyciu energii i jakie działania można podjąć, aby je zminimalizować.
Jak wygląda audyt sprężonego powietrza?
Audyt sprężonego powietrza składa się z kilku podstawowych elementów. Dzięki wykonaniu wszystkich kroków audyt i jego wyniki są kompletne oraz wiarygodne. Przeprowadzenie audytu sieci sprężonego powietrza należy rozpocząć od zbadania pracy sprężarek poprzez pomiar ich obciążenia. Następnym krokiem audytu jest wykonanie pomiaru przepływu sprężonego powietrza. Odbywa się to przy pomocy sondy umieszczonej w rurociągu instalacji. Sonda ta mierzy ilość powietrza przepływającego przez wszystkie elementy układu i określa jego wydajność.
Należy również dokonać pomiaru ciśnienia oraz pomiaru ciśnieniowego punktu rosy. Ostatnią czynnością jest detekcja wycieków sprężonego powietrza. Na koniec następuje interpretacja wykonanych pomiarów i przedstawienie wyników. Dzięki temu otrzymujemy kompletną i konkretną informację na temat stanu sieci sprężonego powietrza.
Jakie korzyści wiążą się z wykonaniem audytu sprężonego powietrza?
Sprężone powietrze jest bezpiecznym i wydajnym, ale drogim medium roboczym. Energia elektryczna zostaje przetworzona w sprężone powietrze jedynie w 15-20%. To sprawia, że wszelkie usterki czy nieszczelności w systemie prowadzą do dużych strat finansowych, zmniejszenia wydajności układu, a w skrajnych przypadkach – do nieprawidłowego działania zastosowanych urządzeń pneumatycznych.
Wykonanie audytu sprężonego powietrza niesie za sobą szereg korzyści, w tym również takie czynności jak:
- dokonanie prawidłowego doboru urządzeń,
- wykonanie prawidłowego projektu instalacji,
- sprawdzenie nieszczelności w kluczowych miejscach instalacji,
- kontrola właściwej objętości ciśnieniowej dla podtrzymania optymalnej wydajności,
- stopień zużycia kompresorów oraz urządzeń przyłączonych do instalacji.
Jakie elementy i parametry instalacji pneumatycznej podlegają audytowi?
Najważniejsze elementy audytu instalacji sprężonego powietrza to:
- Badanie pracy sprężarek – w trakcie kontroli wykonuje się pomiar obciążenia pracy układów kompresorów. Na każdą sprężarkę można założyć jednostkę pomiarową, żeby otrzymać kompletny wynik. Praca urządzeń jest mierzona przez odpowiednio długi okres, np. przez tydzień. Sprawdza się m.in. drgania, zużycie łożysk, temperaturę i rozkład ciepła czy obroty.
- Pomiar przepływu sprężonego powietrza – w rurociągu instalacji umieszcza się sondę, która mierzy ilość powietrza przepływającego przez wszystkie elementy instalacji, a tym samym określa wydajność systemu. Jeśli chcemy otrzymać obraz sytuacji z całego zakładu przemysłowego, pomiar przepływu sprężonego powietrza trzeba przeprowadzić we wszystkich punktach pomiarowych jednocześnie.
- Pomiar ciśnienia – jest zwykle połączony z pomiarem przepływu sprężonego powietrza i pozwala na zbadanie, w jakich momentach występują spadki ciśnienia. To badanie również wykonuje się w kilku punktach jednocześnie. Poznajemy dzięki niemu dolne i górne graniczne ciśnienie, które włącza lub wyłącza kompresory.
- Pomiar punktu rosy – w rurociągu umieszcza się sondę punktu rosy, która mierzy wartości temperatury, przy której para wodna w sprężonym powietrzu zacznie się skraplać. Do jej pomiaru służą mobilne lub stacjonarne mierniki punktu rosy. Wartość ta ma decydujący wpływ na poprawny przebieg procesów produkcyjnych.
- Detekcja wycieków sprężonego powietrza – nieszczelności to problem większości instalacji sprężonego powietrza, przez który pieniądze dosłownie się ulatniają. Dzieje się tak, ponieważ wydostający się strumień powietrza jest niesłyszalny i niewidzialny. Spowodowane przez to straty finansowe mogą być ogromne.
FAQ:
1. Czy audyt sprężonego powietrza się opłaca?
Audyt układu sprężonego powietrza przyczyni się do poprawy efektywności energetycznej i redukcji kosztów operacyjnych.
2. W jakim celu wykonuje się audyt sprężonego powietrza?
Celem przeprowadzenia audytu sprężonego powietrza jest zmniejszenie zużycia energii elektrycznej potrzebnej na wytwarzanie sprężonego powietrza w zakładzie.
3. Kiedy robić kontrolę sprężonego powietrza?
Zaleca się, aby kontrolę sprężonego powietrza przeprowadzać jak najczęściej, nawet codziennie. Pozwoli to utrzymać maszyny w dobrej kondycji i na bieżąco kontrolować jakość sprężonego powietrza.