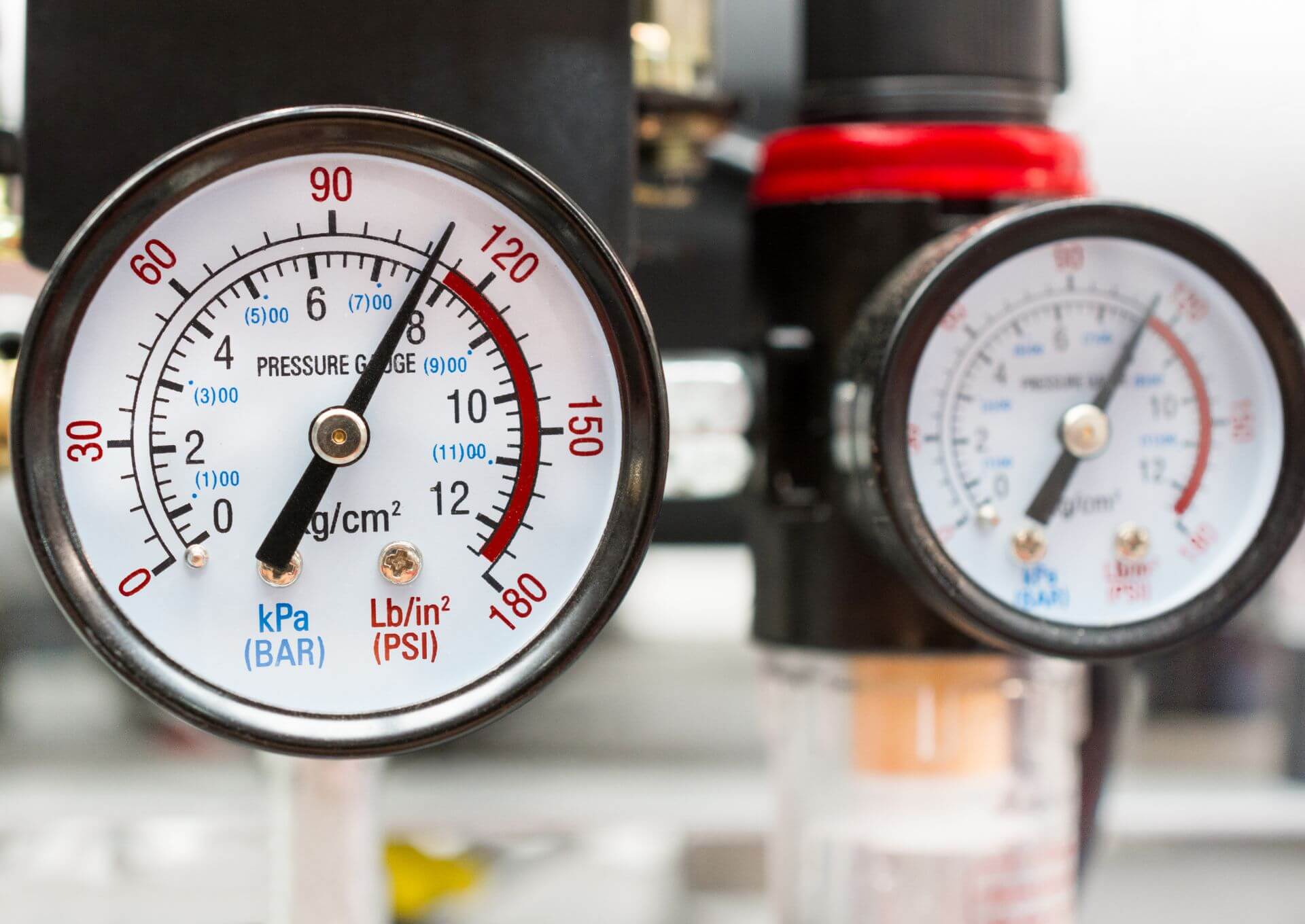
Odpowiednie ciśnienie powietrza w instalacji pneumatycznej jest jednym z najważniejszych wyznaczników efektywnej pracy systemu, w którym w roli medium wykorzystuje się sprężone powietrze – a do tego niezbędny jest odpowiedni sprzęt. Jaki manometr wybrać do kompresora? Na jakie rodzaje dzielimy manometry sprężarkowe? Wyjaśniamy!
Jaki manometr do sprężarki? Rodzaje i zasady działania
Manometry to duża i różnorodna grupa urządzeń niezbędnych zasadniczo w każdej instalacji przemysłowej – są potrzebne kompresorom, pompom, ale także układom hydraulicznym czy systemom chłodzenia, a więc w systemach sprężonego powietrza, hydraulice, gazownictwie i ciepłownictwie, a nawet w gospodarstwach domowych. Z tego względu powstało wiele wariantów manometrów – o różnym sposobie działania, budowie, parametrach i zastosowaniach. Wszystkie te urządzenia łączy tylko wspólna funkcja: wykorzystanie do pomiaru ciśnienia względem ciśnienia otoczenia, najczęściej atmosferycznego, oraz utrzymania go na właściwym poziomie.
W technice pomiarowej w różnych gałęziach przemysłu stosuje się przede wszystkim manometry ze sprężystymi elementami pomiarowymi – z rurką Bourdona, membraną lub puszką.
Manometry z rurką Bourdona i manometry glicerynowe
W tego typu manometrach elementem pomiarowym jest rurka Bourdona – czyli sprężysta metalowa rurka o poprzecznym, spłaszczonym przekroju.
Z jednej strony rurka jest przymocowana do obudowy, dzięki czemu doprowadza do niej ciśnienie. Drugi jej koniec łączy się z układem wskazującym pomiar ciśnienia – z układem przekładni. Pod wpływem różnicy między ciśnieniem wewnętrznym i zewnętrznym wygięta rurka Bourdona prostuje się i zamontowana na jej końcu dźwignia przenosi odkształcenie elementu na mechanizm zębatkowy, czyli ruch obrotowy wskazówki manometru. Wskazanie urządzenia odczytuje się na tarczy z podzielną skalą.
Ten typ manometru jest wykorzystywany w przemyśle najczęściej, bo dzięki wielu wariantom można dopasować go do odmiennych warunków pracy – w tym mediów zanieczyszczonych bądź agresywnych (w przemyśle petrochemicznym, farmaceutycznym). Zazwyczaj jednak stosuje się je w układach sprężonego powietrza, hydrauliki wodnej i siłowej czy też gazów medycznych oraz przy mediach płynnych i gazowych, które nie są gęste, lepkie lub krystaliczne.
Problem występowania drgań w instalacji rozwiązują specjalne manometry glicerynowe. Wypełnienie osłabia wibracje, zatem odczyt jest precyzyjny. Jest to rozwiązanie zaprojektowane m.in. dla przemysłu morskiego, ale też różnego rodzaju pomp czy pojazdów.
Manometry z rurką Bourdona sprawdzają się do pomiaru ciśnienia w dużym zakresie i także w przypadku bardzo wysokich ciśnień, nawet do 7000 bar.
Manometry membranowe
W tego typu manometrach element pomiarowy stanowi sprężysta membrana – przepona zamocowana szczelnie w obudowie. Wokół membrany znajduje się dwuczęściowy korpus, którego dolna część tworzy komorę pomiarową, a w górnej części panuje ciśnienie atmosferyczne. Mierzone ciśnienie oddziałuje na jedną stronę membrany oraz powoduje jej ugięcie, proporcjonalne do różnicy, jaka występuje pomiędzy nim a ciśnieniem atmosferycznym. A ruch membrany skutkuje przemieszczeniem się cięgła, które porusza przekładnią wskazówki.
Manometry membranowe są stosowane do pomiaru ciśnienia w zakresie od 0 ÷ 16 mbar do 0 ÷ 40 bar. Mogą mierzyć ciśnienie mediów agresywnych, lecz wtedy membrana musi być odpowiednio dostosowana: powleczona tantalem czy tytanem.
Manometry puszkowe
Manometry puszkowe są przeznaczone do precyzyjnego pomiaru bardzo niskich ciśnień i podciśnień – od 0 ÷ 2,5 mbar do 0 ÷ 0,6 bar. Stosuje się je m.in. w hutnictwie, gazownictwie, energetyce oraz w przemyśle medycznym, w tym do monitorowania filtrów, i wyłącznie w przypadku mediów gazowych suchych. Element pomiarowy tego rodzaju manometru to tzw. puszka – utworzona z połączenia dwóch membran. W jednej z nich znajduje się otwór, którym doprowadzane jest ciśnienie. Wewnętrzna część puszki kurczy się lub rozszerza, a wartość jej ugięcia przekłada się na ruch obrotowy, który umożliwia odczyt na tarczy manometru.
Jaki manometr wybrać do kompresora?
Manometry dopasowuje się precyzyjnie do modelu kompresora, rodzaju medium i jego parametrów, wartości ciśnienia oraz warunków zewnętrznych, czyli w praktyce należy zwrócić uwagę na kilka elementów.
- Ciśnienie medium. W tym przypadku ważny jest rodzaj i model manometru – manometr z rurką Bourdona stosuje się zarówno do niskich, jak i do bardzo wysokich ciśnień (od 0 ÷ 0,6 bar do 0 ÷ 7000 bar), z kolei puszkowe wyłącznie do najniższych wartości (od 0 ÷ 2,5 mbar do 0 ÷ 0,6 bar).
- Rodzaj medium i warunki. Do agresywnych, zanieczyszczonych mediów i w wysokich temperaturach stosuje się manometry odpowiednio przygotowane na takie warunki, wykonane ze specjalnych materiałów lub z uwzględnieniem dodatkowych części, np. powłok z tytanu czy elementów ze stali nierdzewnej.
- Klasa dokładności. Jest różna zarówno pomiędzy samymi rodzajami, jak i modelami manometrów. Standardowo klasa dokładności dla omawianych w artykule manometrów wynosi 0,1 do 2,5%, co pozwala na precyzyjny pomiar. Wartość ta określa granicę błędu i jest wyrażona jako procent całego zakresu.
- Montaż manometru. Bardzo ważna jest średnica i wielkość gwintu, a także sam sposób montażu manometru. W manometrach stosuje się także dwa typy przyłącza – tylne (axialne) i dolne (radialne) o różnych średnicach.
Wybór manometru do kompresora jest niezwykle ważny, dlatego warto skonsultować się ze specjalistą – zachęcamy do kontaktu z Almiair.pl, a indywidualnie doradzimy i opowiemy o najnowszych rozwiązaniach.
FAQ:
- Do czego służy manometr do kompresora?
Manometr do kompresora służy do mierzenia (i utrzymywania) ciśnienia względem ciśnienia otoczenia, najczęściej atmosferycznego.
- Jakie są rodzaje manometrów do kompresora?
Podstawowy podział urządzeń względem sposobu działania obejmuje manometry z rurką Bourdona (tzw. standardowe), manometry membranowe i puszkowe, które są urządzeniami analogowymi. Na rynku dostępne są też manometry cyfrowe.
- Jaki manometr przemysłowy wybrać?
Wybór manometru do zastosowań przemysłowych zależy od kilku kwestii – to zakres ciśnień (indywidualny dla rodzaju i modelu urządzenia), rodzaj i specyfika medium, warunki zewnętrzne (zwłaszcza temperatura) i wymagana klasa dokładności.