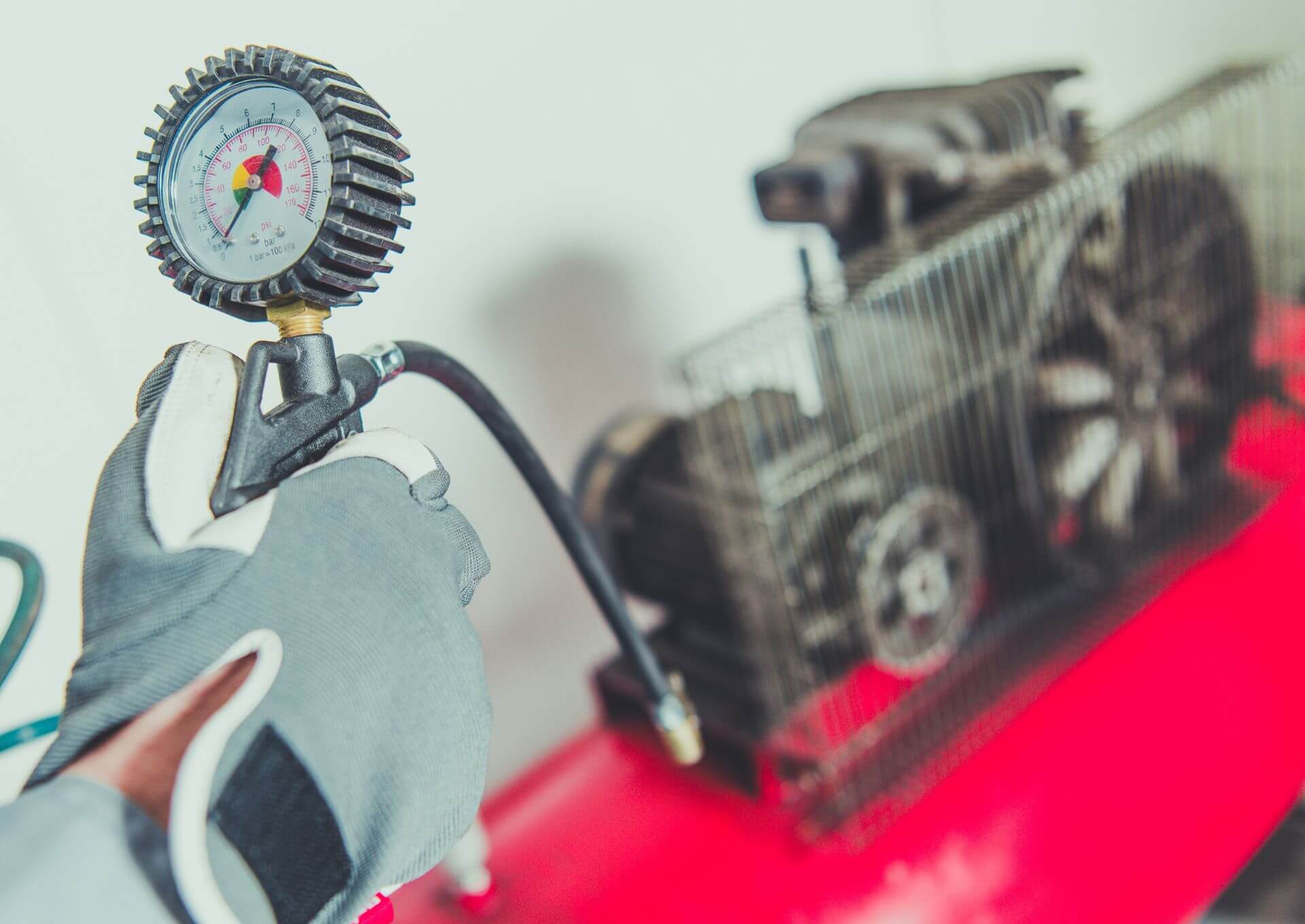
Sprawdzenie szczelności instalacji pneumatycznej jest niezwykle istotne – ma zapewnić jej prawidłowe funkcjonowanie. Główną rolę odgrywa tam sprężone powietrze, dostarczane do różnych narzędzi i maszyn. Każde pęknięcie może prowadzić do poważnych problemów, ponieważ ulatanie się tego medium zmniejsza wydajność całego systemu. Ponadto zwiększają się koszty eksploatacji, a taka sytuacja bywa też zagrożeniem dla bezpieczeństwa pracy oraz osób przebywających w pobliżu instalacji.
Czym jest instalacja pneumatyczna?
Instalacja pneumatyczna to system wykorzystywany w wielu dziedzinach przemysłu. Kompresor powietrza jest tutaj połączony przewodami i rurami z zamontowanymi odbiornikami. Są nimi narzędzia pneumatyczne, napędzane przez sprężone powietrze. Mogą być to na przykład szlifierki, wkrętarki, klucze, polerki czy młoty.
Jakie zastosowanie ma sprężone powietrze?
Warto wiedzieć, że sprężone powietrze jest przez niektórych uznawane za najdroższe medium. Zawdzięcza to swojej wszechstronności, pozwalającej na użycie go w naprawdę różnych branżach.
W branży spożywczej systemy tego typu są bardzo cenione. Sprężone powietrze wykorzystuje się tam do napędzania maszyn do pakowania i osuszania produktów oraz mieszania składników. Używa go także motoryzacja i przemysł budowlany, gdzie specjaliści posługują się narzędziami zasilanymi przez sprężone powietrze.
Dlaczego szczelność instalacji pneumatycznej jest ważna?
Nieszczelności w instalacji pneumatycznej mogą prowadzić do spadku ciśnienia. Bywa to szczególnie martwiące, ponieważ nawet niewielkie wycieki nierzadko znacząco obniżają ten parametr – jest on przecież niezbędny do prawidłowego działania narzędzi i maszyn pneumatycznych. Taka sytuacja może skutkować złą wydajnością całego systemu. To z kolei wiąże się ze zwiększeniem czasu pracy urządzeń czy z występowaniem opóźnień w procesach produkcyjnych.
Nieszczelności prowadzą do utraty sprężonego powietrza, co zmusza sprężarkę do częstszej i dłuższej pracy w celu utrzymania wymaganego ciśnienia. Jest to bezpośrednio związane z dużą eksploatacją energii elektrycznej – sprężarka zużywa jej więcej, aby zrekompensować straty. To wszystko przekłada się na wyższe koszty utrzymania systemu.
Jak sprawdzić szczelność instalacji pneumatycznej?
Wszelkie niecodzienne dźwięki, takie jak syk czy gwizd, powinny budzić niepokój i mogą wskazywać na potencjalne problemy z systemem. Pamiętaj jednak, że wiele nieszczelności w instalacji pneumatycznej jest po prostu niesłyszalnych dla ucha ludzkiego. Dlatego też baczna obserwacja oraz monitorowanie parametrów ma tutaj ogromne znaczenie.
Jednakże w takim przypadku, by dokładnie ocenić sytuację, konieczne będzie przeprowadzenie profesjonalnej próby szczelności instalacji pneumatycznej. Tego typu testy pozwalają na wykrycie nawet najmniejszych pęknięć, które mogą umknąć zwykłej obserwacji lub słuchowi ludzkiemu.
Próby szczelności instalacji sprężonego powietrza
Próba szczelności jest kluczowym procesem, pozwalającym na weryfikację integralności systemu pneumatycznego. Całe badanie polega na wypełnieniu instalacji sprężonym powietrzem pod odpowiednim ciśnieniem.
Najpierw jednak konieczne jest odłączenie narzędzi pneumatycznych związanych z systemem. W innym przypadku wyniki będą niemiarodajne. Z tego względu właśnie badanie to zwykle przeprowadza się po zakończeniu pracy zakładu – instalacja nie może być używana podczas testu, a przestoje w produkcji nie są przecież mile widziane.
Jak sprawdzić szczelność instalacji sprężonego powietrza? Dalszy przebieg próby
Czas przystąpić do podłączenia manometru – urządzenia, które pozwala na bardzo dokładne pomiary ciśnienia w danym systemie. Kiedy sprzęt znajdzie się już w odpowiednim miejscu, instalację pneumatyczną wypełnia się sprężonym powietrzem.
Jaki będzie następny krok? Teraz pozostaje poczekać 24 godziny. Jednakże ważne jest, by w tym czasie nie korzystać z systemu. To konieczny warunek, żeby cały test zakończył się miarodajnym wynikiem.
Próba szczelności – jak interpretować jej wyniki?
Jeśli po upływie 24 godzin spadek ciśnienia wynosi powyżej 0,1 bara, to próba kończy się niepowodzeniem – instalacja jest nieszczelna. W takiej sytuacji należy oddać sprawę w ręce specjalistów. Profesjonaliści zajmą się szukaniem oraz usuwaniem nieszczelności, by przywrócić systemowi jego pełną funkcjonalność.
Próba szczelności instalacji sprężonego powietrza – o tym należy pamiętać
Podczas przeprowadzania próby szczelności instalacji sprężonego powietrza niezwykle ważne jest przestrzeganie wszelkich procedur. Zapewnienie bezpiecznego środowiska pracy nie tylko chroni personel przed potencjalnymi zagrożeniami, ale także gwarantuje rzetelność i skuteczność samej próby.
Po zakończeniu badania, bez względu na jego wynik, sporządza się specjalny protokół. Dokument ten stanowi potwierdzenie wykonania testu i jego wyników. Jest to ważne dla dalszego utrzymania i zarządzania systemem pneumatycznym.
FAQ:
1. Dlaczego sprawdzenie szczelności instalacji pneumatycznej jest tak ważne?
Sprawdzenie szczelności instalacji pneumatycznej jest ważne, ponieważ każda nieszczelność może prowadzić do poważnych problemów. Są to między innymi takie sytuacje jak spadek ciśnienia, zmniejszona wydajność całego systemu, zwiększone koszty eksploatacji oraz potencjalne zagrożenie bezpieczeństwa pracy.
2. Jakie są pierwsze podejmowane kroki podczas przeprowadzania próby szczelności instalacji sprężonego powietrza?
Pierwszym i niezwykle istotnym krokiem jest odłączenie narzędzi pneumatycznych związanych z systemem – dlatego też przeprowadzenie badania najczęściej ma miejsce po zakończeniu pracy zakładu, aby uniknąć przestojów produkcyjnych. Następnie montuje się manometr do systemu, który dokładnie zmierzy ciśnienie.
3. Jak interpretować wyniki próby szczelności instalacji sprężonego powietrza?
Jeśli po upływie 24 godzin spadek ciśnienia wynosi powyżej 0,1 bara, oznacza to, że instalacja jest nieszczelna i wymaga interwencji specjalistów. Zajmą się oni poszukiwaniem i naprawą pęknięć. W przeciwnym wypadku system uznaje się za szczelny.